From recycling to production: bringing the EV battery supply chain to the US
Did you know SHIFT is taking the stage this fall ? Together with an amazing line-up of experts, we will explore the future of mobility during TNW Conference 2021. Secure your ticket now!
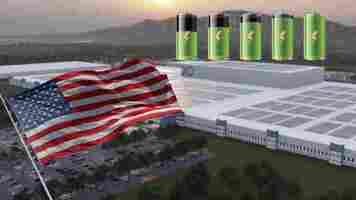
Even though the transition to battery electric vehicles is at an early stage, we’re well aware of the need to recycle and reuse the precious metals and materials contained within lithium-ion batteries.
Among the US recycling companies, Redwood Materials has emerged as a very competitive player, since its founding in 2017 by J.B. Straubel. Interestingly, Straubel revealed to Bloomberg that his company’s aim goes beyond recycling to bringing the battery supply chain from Asia to the US.
Before Redwood, most US recycling companies simply ground up the batteries into a crude powder known as “black mass” for easy transportation. Then, they shipped those materials overseas to be refined and processed, according to Jeffrey Spangenberger, director of the Department of Energy’s ReCell Center .
However, this process has two disadvantages: the environmental impact of the materials’ transportation, and the dependence on foreign suppliers.
“We want to buy these materials once and then keep them here,” Spangenberger said. “The recycler and the manufacturer together — if that can be done under one roof, then we’re answering two questions at once.”
The company wants to do away with the 80,000 kilometer (50,000 miles) supply chain of battery components, which are needed for the final production of an EV battery in the US.
For this reason, Redwood is seeking three types of operation: recycling, manufacturing copper foils for anodes, and producing cathodes.
Recycling is already taking place at the factory in Carson City, Nevada, where the company has its headquarters.
Redwood has also starting working on a second factory in Nevada to manufacture the delicate copper foils of anodes (the negative terminal of the battery), which are in short supply.
However, the production of cathodes (the positive terminal of the battery) is by far the most significant addition.
First, the cathode is the most expensive part of the battery. Some 10% to 30% of a cathode is made from cobalt, priced at approximately $28,500 per ton. This makes cobalt the priciest element of a cathode, more expensive than nickel, manganese, and aluminum combined.
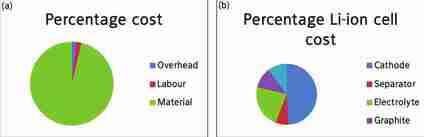
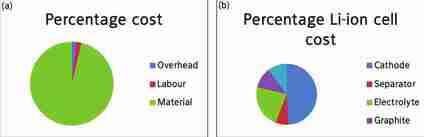
Secondly, the cathode is also the most pollutant part of the battery. The mining of the raw materials that comprise it, their virgin refinement, and their transportation overseas not only increase production costs dramatically, but also increase greenhouse emissions.
Straubel is searching for a new location in Nevada to build a new million-square-foot factory. He explains that the plant will produce enough cathode material for 100 gigawatt hours of batteries a year by the end of 2025.
This translates to about 1.3 million long-range vehicles annually, which matches the capacity of the biggest producers in Asia.
The company’s big target means that it can’t solely rely on recycled elements. Its aim, therefore, is to use 50% recycled and 50% raw materials.
Currently, EV batteries account for less than 10% of Redwood’s recycling stock, but the retired batteries from consumer electronics are abundant.
Nevertheless, even with 50% of recyclable materials, the consolidation of the supply chain in the US would have a tremendously positive environmental impact. According to BloombergNEF’s analyst James Firth, it would reduce the emissions from battery-pack manufacturing by at least 41%.
Straubel believes that in the next decades recycled materials will be used for almost 100% of the world’s battery production. And if he’s right, not only would batteries become more affordable, but also make their production — which still raises concerns — significantly greener.
Do EVs excite your electrons? Do ebikes get your wheels spinning? Do self-driving cars get you all charged up?
Then you need the weekly SHIFT newsletter in your life. Click here to sign up.
Adieu, Europe! China takes top spot for green car sales in 2021
After being overtaken by Europe in 2020, China is back on top and leading the charge in new energy vehicle (NEV) global sales
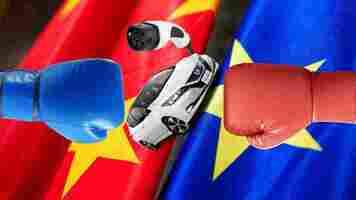
According to Chinese EV media outlet CnEVPost , China sold 3.31 million NEVs (battery electric vehicles, plug-in hybrids, and fuel cell vehicles) out of a 6.23 million global total in 2021 . Based on data from the China Passenger Car Association (CPCA), t his means that China took a 53% share of the global market, surpassing Europe’s 33% and the US’s 11%.
These figures align closely with the findings of the International Energy Agency (IEA), published in late January.
According to the IEA, global NEV sales were slightly higher, at 6.6 million units. China finished 2021 with 3.4 million NEV registrations, which would account for a 51.5% share of the global market. This is 1.5% less than the CPCA’s figures.
And while it’s difficult to verify the data of both agencies, there’s one conclusion we can make: China trampled all over Europe last year.
The CPCA’s analysis indicates that 2020 was a rough year for China, which allowed Europe to take the global market lead for the first time, reaching 44% of NEVs sold.
In contrast, China’s market share dropped to 41%, even though it held a dominant position between 2016 and 2019.
The CPCA attributes this slump to two main reasons: revamped environmental policies and the COVID pandemic.
And this sounds rather accurate.
In 2020, China reduced the number of EVs and hybrids eligible for subsidies, and stopped providing them for fuel cell vehicles entirely. On the other side of the world, most of European countries were offering tax breaks and purchasing incentives to attract consumers to electric machines.
And while China was the first nation to be hit by the pandemic — and the first to deal with manufacturing setbacks — the outbreak’s consequences made an appearance in Europe some months later.
For now, it looks like China’s back on track. The battle is far from over — and the coming years will show if it continues its EV dominance, or if other continents can catch up.
HYDROGENUNDI?! Hyundai’s commercial vehicles will all be hydrogen-powered by 2030
Did you know SHIFT is taking the stage this fall ? Together with an amazing line-up of experts, we will explore the future of mobility during TNW Conference 2021. Secure your ticket now!
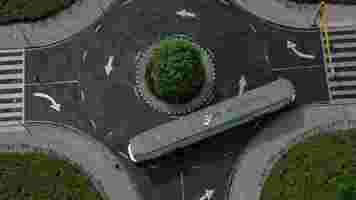
While other carmakers showed off their latest concept cars at IAA Mobility in Munich , Hyundai had another focus. It announced its Hydrogen Vision 2040 at an online event called Hydrogen Wave . The company’s mighty aim is to become the first automaker to apply fuel cell systems to all commercial vehicle models by 2028.
Besides exciting new fuel cell technology, Hyundai also shared its prototypes for new transportation designs and mobility solutions.
Hyundai offers a game-changer for shipping and logistics
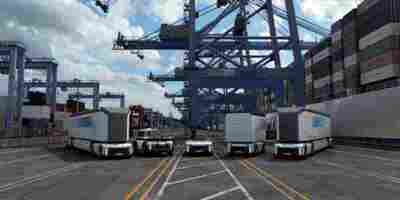
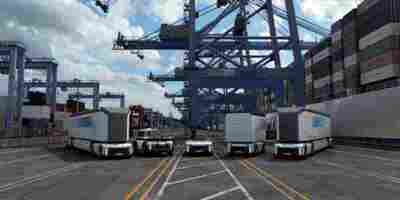
The South Korean automaker unveiled the “Trailer Drone” concept, a hydrogen-powered autonomous container transportation system that can operate fully autonomously at a duration of 1,000km on a single charge.
Beyond the long-distance capabilities, the combination of the Trailer Drone with the Fuel Cell e-Bogie is where things really get interesting.
Ok, so what the heck is an e-Bogie?
The term “bogie” originates from the rail industry. Rail bogies are wheel subframes that sit under every train car. The Fuel Cell e-Bogie sits under the truck container, just like a rail bogie.
The e-Bogie can perform a turn in place and diagonally “crab walk,” thanks to four-wheel independent steering and low-profile design that allows it to carry a small shipping container or other loads.
Placing two e-Bogies on top of each end of a full-sized semi-trailer creates a Trailer Drone. This is an autonomous trailer capable of piloting itself around shipping yards, highways, and urban centers. It includes dual independent steering at both ends, making it easy to navigate tight bends and small roundabouts.
Transport operators can configure a ‘Cluster Mode’ to enable multiple Trailer Drones to travel together in an almost train-like configuration.
Hyundai sees the Fuel Cell e-Bogie as a multi-purpose platform for future use in ground logistics, construction, firefighting, and disaster relief missions.
They shared a prototype Rescue Drone that combines a drone and a Fuel Cell e-Bogie to create a flying drone for remote and autonomous use in critical operations such as fire-fighting and life-saving. It achieves a 450 to 500km driving range on a single charge.
Time for another Hydrogen powered-car
During Hydrogen Wave , the company also shared details about its high-performance sports car, the Vision FK. It has an output of around 670 horsepower, and Hyundai claims the vehicle can reach 0-100 km/h in under four seconds. The car combines hydrogen with a plug-in system and rear-while drive to deliver a range of over 600km. Hyundai revealed no production timelines.
It’s nice enough, but not the most exciting news of the event.
The third-generation fuel cell stack
Hyundai also shared news of the third-generation fuel cell stack to succeed NEXO’s current stack. There are two power versions. The 100kW is 30% smaller than its predecessor, making it suitable for different vehicle types. The 200kW is designed for commercial vehicles, and its power output has doubled — an impressive feat.
Furthermore, the third-generation fuel cell stack price will be dramatically reduced — with projections of over 50% — critical for FCEVs to reach cost parity with BEVs by 2030.
Large ships or IT companies could also stack the 100kW modular units as an emergency power system.
A long history committed to hydrogen
Hyundai developed its first fuel cell electric vehicle (FCEV) in 1998. In 2013, The Tucson FCEV (ix35 Fuel Cell) was introduced in 2013. Then, in 2018, the company launched the next-generation fuel-cell SUV, NEXO . It takes just five minutes to fill and can drive up to 666kms without charging.
Hyundai first launched their Xcient Fuel-Cell trucks in 2020. They feature a 190-kilowatt fuel cell comprising seven high-pressure tanks holding around 35kg of hydrogen.
The trucks have a long-distance range of about 400km before needing refueling, which far surpasses the capabilities of trucks powered by electric batteries. The fuel cell fully charges in under 20 minutes and can drive for about 250 miles before needing more hydrogen.
The firm plans to put 1,600 hydrogen trucks on Swiss roads by 2025 and has rented its trucks to local companies in Switzerland for almost a year.
The company has also been trialing its hydrogen-powered Elec City Fuel Cell bus in Germany this year.
Looking beyond the road to new hydrogen capabilities
Hyundai plans to launch two new hydrogen fuel cell powertrains in 2023, as part of their broader plan to make hydrogen mainstream by 2040.
This is part of a bigger mission introducing hydrogen fuel cells into high-performance vehicles, urban air mobility, robots, aircraft, and large ships. They see a future when building utilities, urban energy sources, and power plants incorporate hydrogen fuel cell systems into their green energy.
It’s worth remembering that hydrogen has had its critics over time, especially in terms of cost and scale. Yet, Hyundai has remained steadfast to a hydrogen-powered future .
I’ve long contended that the battle to win hearts and minds towards hydrogen will be in the industrial space. Hyundai’s commitment to commercial vehicles, road logistics, and public transport provides a compelling way forward.
You need to look no further than Hyundai for a shining example of a vision-lead company that sees its ideas through, creates new technology, and defines new capabilities.
Do EVs excite your electrons? Do ebikes get your wheels spinning? Do self-driving cars get you all charged up?
Then you need the weekly SHIFT newsletter in your life. Click here to sign up.