US regulator approves first-ever fully autonomous commercial drone flights
The Federal Aviation Administration has approved the first-ever fully-automated commercial drone flights.
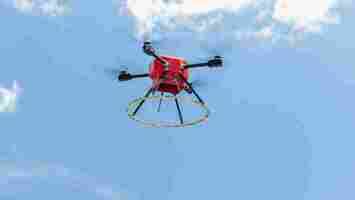
The US aviation regulator has permitted American Robotics to fly its Scout quadcopter beyond the line-of-sight of human operators.
In approval documents recently posted on the FAA website , the agency said the exemption only applies to rural areas, daylight visibility, and altitudes below 400 feet.
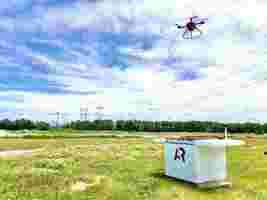
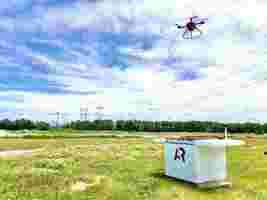
The drones must also have a maximum takeoff weight of 20 pounds and operate solely for the purposes of research and development, crew training, and market surveys.
American Robotics must also designate a remote pilot in command for each flight who “has the ultimate responsibility for the entire flight and must ensure its safety.”
The Massachusetts-based firm nonetheless called the decision “a pivotal inflection point in the commercial drone industry:”
The Scout System uses acoustic Detect-and-Avoid (DAA) technology to keep drones at a safe distance from other aircraft. American Robotics said it demonstrated the safety of the drones during four years of testing across eight states in the US.
The first users will be agricultural operations in Kansas, Massachusetts, and Nevada, according to The Wall Street Journal . But the FAA said the exemption could also demonstrate the benefits of using drones for transportation, mining, technology, and non-durable manufacturing.
If the American Robotics scheme is a success , it could pave the way for a wave of further regulatory approvals for drones.
Researchers are developing robot swarms that turn into buildings, vehicles, and more
There are two schools of thought when it comes to building bridges. There’s the traditional way involving humans assembling materials to create a unique structure. And then there’s the way MIT and the US Army want to do it: you open a box and a bunch of Lego-style construction bricks fly out and turn themselves into a bridge.

When those bricks – actually, more like interlocking snowflakes – get done being a bridge, they could be autonomously reconfigured to suit another need such as becoming a boat or a glider. They could also simply disassemble themselves and return to storage.
This might sound like something out of Neural’s Guide to the Glorious Future of AI , but it’s actually completely grounded in present-day technology.
MIT and a US Army think-tank recently published a research paper detailing the development of a mass-producible, reconfigurable, metamaterial that could be used to create robots made out of robots.
According to the research team:
That’s a long way of saying they’ve created a Lego-style kit of super-strong, easy-to-manipulate materials that can be mass-produced quickly and cheaply.
What started as an Army thought experiment to come up with the quickest, cheapest way for a robot swarm to build a bridge for troops turned into a vein of research with the potential to upend the field of construction.
The core challenge for quick-deploy construction systems is figuring out how to get the most out of each and every scrap of material. Under the current technology paradigm, for example, a small team of soldiers would need a variety of vehicles and external support teams in order to navigate long stretches of multi-faceted terrain.
MIT and the Army’s voxel-based construction system aims to solve this problem. Through the use of special AI-generated shapes at the cellular level, the system’s interlocking voxel pieces are like 3D-printed material that doesn’t require a printer to work with.
What’s even more impressive is once construction is complete, the pieces can be reconfigured into myriad other designs. Per the paper:
While this research is still in its early phases, the ultimate goal is the production of a set of self-assembling AI-powered construction materials in the form of a deployable robot swarm.
In theory, a group of soldiers could radio for a swarm and, somewhere back at the rear echelon, a stack of building blocks would receive the signal and turn itself into an “ultralight lattice aerostructure” that could be dropped into the battlespace via drone. Once on the ground, the materials could follow the soldiers around becoming whatever vehicle, structure, or tool they needed.
You can read the full paper here on ScienceAdvances .
This robot uses color cameras and AI to grab transparent objects
Robots have got pretty good at picking up objects. But give them something shiny or clear, and the poor droids will likely lose their grip. Not ideal if you want a kitchen robot that can slice you a piece of pie.
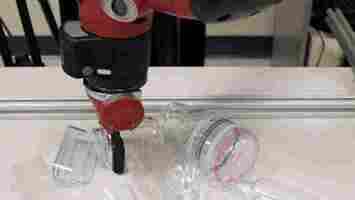
Their confusion often stems from their depth camera systems. These cameras shine infrared light on an object to detect its shape, which works pretty well on opaque items . But put them in front of a transparent object, and the light will go straight through and scatter off reflective surfaces, making it tricky to calculate the item’s shape.
Researchers from Carnegie Mellon University have discovered a pretty simple solution: adding consumer color cameras to the mix. Their system combines the cameras with machine learning algorithms to recognize shapes based on their colors.
The team trained the system on a combination of depth camera images of opaque objects and color images of the same items. This allowed it to infer different 3D shapes from the images — and the best spots to grip.
The robots can now pick up individual shiny and clear objects, even if the items are in a pile of clutter. Check it out in action in the video below:
The team admits that their system is still far from perfect. “We do sometimes miss, but for the most part it did a pretty good job, much better than any previous system for grasping transparent or reflective objects,” said David Held , an assistant professor at CMU’s Robotics Institute.
I’m still not sure I’d trust it with a razor-sharp kitchen knife. Unless I was really hungry and unwilling to leave the couch.